Introduction
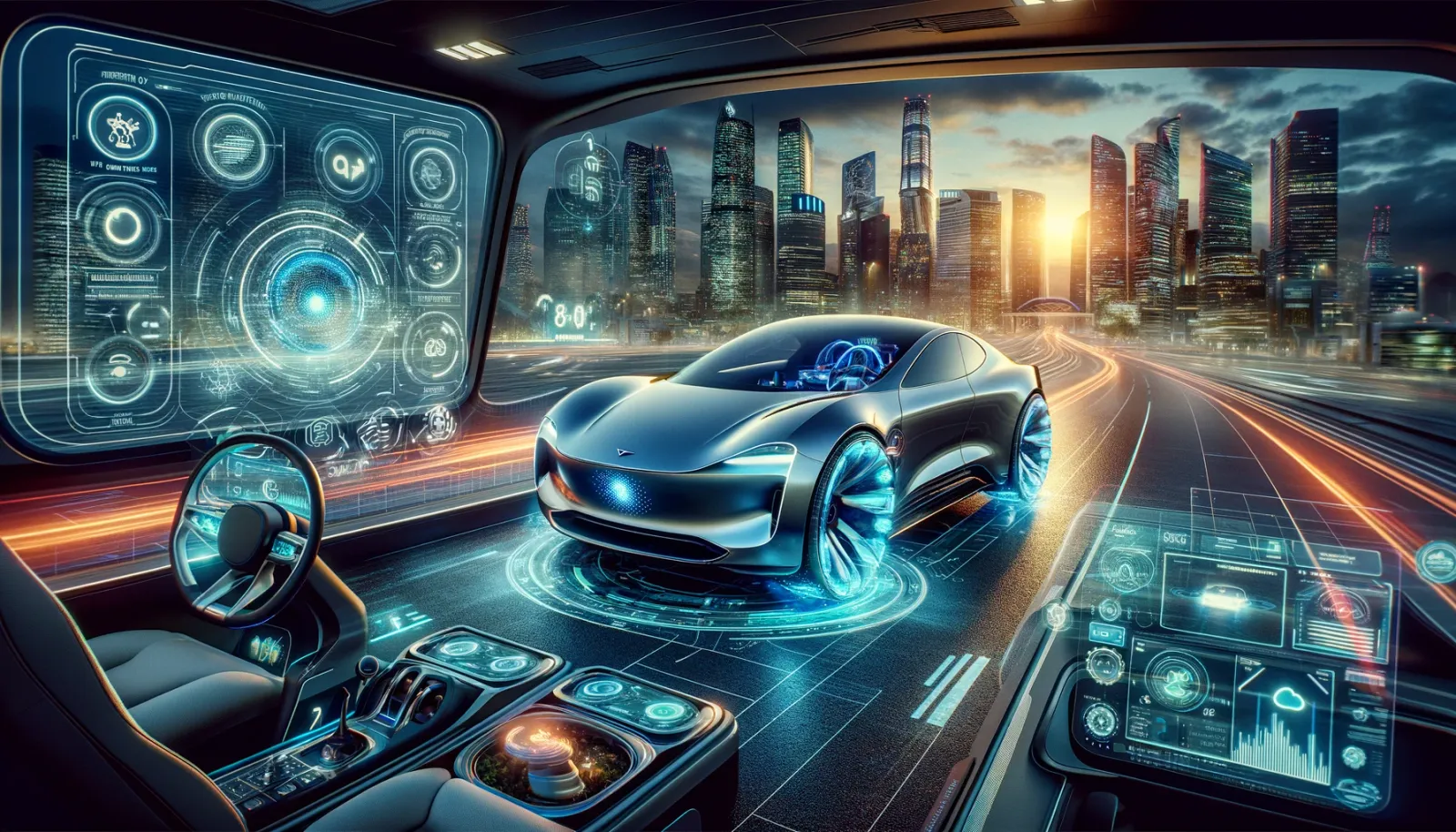
It's worth noting from the outset that the article's headline is somewhat clickbait-driven, thanks to the buzzword "Software Defined Vehicle". This article does not aim to provide a universally accepted definition of SDV or enumerate the benefits that an automaker will gain from this technology, as this has already been done countless times before. Instead, we propose considering the broader concept of SDV. Essentially, this is the concept of the next-generation vehicle, which is exactly how SODA interprets the term SDV.
Why do we believe this is the correct perspective? The answer lies in analyzing consumer expectations for future vehicles. After all, it is the need to meet these consumer demands that drives innovation and technological shifts in the automotive industry. It is already apparent that these demands define a broader range of vehicle capabilities than what can be offered by merely transitioning to a software defined architecture.
Consumer Demands for Next-Generation Vehicles
So, what should the expanded concept of SDV include from the consumer's perspective:
-
Upgradeability: Automakers are tasked with the ongoing goal of adding value to vehicles after sale, meeting consumer expectations for continuous feature enhancements without hardware upgrades and without the need for physical service visits. Much like smartphones that receive regular updates to enhance functionality and security, next-generation vehicles are designed for over-the-air (OTA) updates. Simply put, consumers expect their cars to continually improve, thanks to the continuous delivery of valuable new software features and updates throughout their lifetime.
-
Personalized Experience: Consumers desire to feel acknowledged as they enter a vehicle tailored to their needs, marking a significant shift from the impersonal nature of traditional cars. With the integration of advanced AI algorithms and cloud connectivity, next-generation vehicles are poised to create individualized driver profiles. These profiles could offer real-time recommendations, from optimal routes to personalized entertainment options, transforming the car into living spaces on wheels. This demand gains additional significance in the context of a potential shift from car ownership to shared vehicle use, facilitating effortless customization for each driver. Personalization should also include vehicle adjustments for various road conditions. For instance, the car's steering, braking, engine performance, tire pressure, and other features could be fine-tuned to optimize performance in winter driving conditions.
-
Improved Safety and Efficiency: Consumers expect enhanced safety and efficiency in their transportation experiences, and V2X technology effectively addresses these expectations. It enables real-time communication between vehicles and infrastructure, leading to accident avoidance and reduced fatalities, thus meeting consumer demands for improved safety. Even when other vehicles or infrastructure elements obscure a driver’s view of vulnerable road users, V2X can alert the driver to their presence. The ability to see through other car sensors creates the ‘networking effect of safety’—that means we are no longer driving only with our car’s sensors, which all need to see the object to detect it, we don’t need to be in the line of sight with the objects. Thereby, V2X enhances efficiency by reducing traffic congestion, improving traffic flow, and decreasing fuel consumption and emissions, aligning with consumers' desires for smoother and more environmentally friendly journeys.
-
Autonomous Driving: Despite the seemingly high-tech capabilities of cars today, the majority of vehicles are actually only at Level 2 in terms of automation. At this point, some successes in implementing Level 3-4 autonomy can be highlighted. For instance, Japan has launched Level 4 driverless transportation services in Eiheiji, and Mercedes-Benz has introduced Level 3 autonomous driving features in its vehicles, with aspirations for Level 4 by 2030. Or Hyundai is intensely working on developing Level-3 autonomous driving technology, aiming to deploy a system specifically for highway driving in the South Korean market. Similarly, autonomous parking systems have received approval in Germany, and other automakers are exploring Level 4 capabilities for their future models. However, this is far from enough to meet the consumer's expectations for the car of the future. The prospect of fully autonomous driving is closer than ever in the eyes of the consumer. This leap forward not only revolutionizes how we perceive personal transport but also significantly enhances safety and efficiency on our roads.
-
Infotainment and Beyond: Both drivers and passengers expect a high level of comfort and entertainment while driving a car. The vehicle should provide access to AI-based voice assistants, streaming services, social networks, and other cloud services. Additionally, vehicle-to-cloud connectivity enables seamless integration with smart home devices and applications. Users can remotely monitor and control their electric cars, pre-condition the cabin temperature before entering the vehicle, and receive notifications regarding charging status and maintenance requirements. Or the vehicle could find and propose a route to the nearest gas station when the car needs fuel. Enhanced comfort should extend beyond the driver to encompass all passengers. For example, the vehicle, using V2X technology, could communicate with smartwatches to monitor the health conditions of children in the back seat, predicting potential motion sickness based on road curvature and driving speed. In response, the vehicle could modify the automated driving style, adjust window settings, and control the air conditioning to maximize comfort and reduce motion sickness.
-
Enhanced Performance and Maintenance: Consumers expect next-generation vehicles not only to offer personalized experiences and efficiency but also to significantly enhance their vehicle maintenance capabilities and improved performance. Cloud computing allows automotive manufacturers to leverage advanced analytics and machine learning algorithms to extract valuable insights from vast amounts of vehicle data. By collecting real-time data from sensors, cameras, and other sources, vehicles can continuously send information to the cloud for analysis. This data-driven approach enables automakers to optimize vehicle performance, predict maintenance requirements, and improve fuel efficiency. For example, vehicle can communicating with a smart grid, scheduling its charging during off-peak electricity usage. This interaction optimizes energy use and maximizes cost efficiency. The car is no longer just a consumer of energy but also an intelligent participant in the wider energy ecosystem.
-
Ongoing Demand for New Features: Consumers expect the rapid deployment of advanced functionalities, especially those that enhance safety, connectivity, and automation. They seek immediate gratification from their vehicles, expecting swift updates and personalization similar to what they're accustomed to with their digital devices. This demand extends not only the introduction of new features but also the continuous improvement and customization of existing features based on consumer feedback, allowing their vehicle's capabilities to evolve over time. However, consumers anticipate more than just innovative features; they also expect these enhancements and new capabilities to be introduced much more quickly than what traditional automotive development cycles have historically permitted. The ability of manufacturers to rapidly bring these innovations to market can significantly influence consumer choice and foster brand loyalty.
So, we have identified the most significant demands, from the user's perspective, for the SDV of the next-generation. Going forward, we will continually refer back to them as our objectives and consider ways to achieve them in terms of necessary changes in both the vehicle development and manufacturing processes and the architecture of the vehicles themselves.
Empowering the Automotive Industry
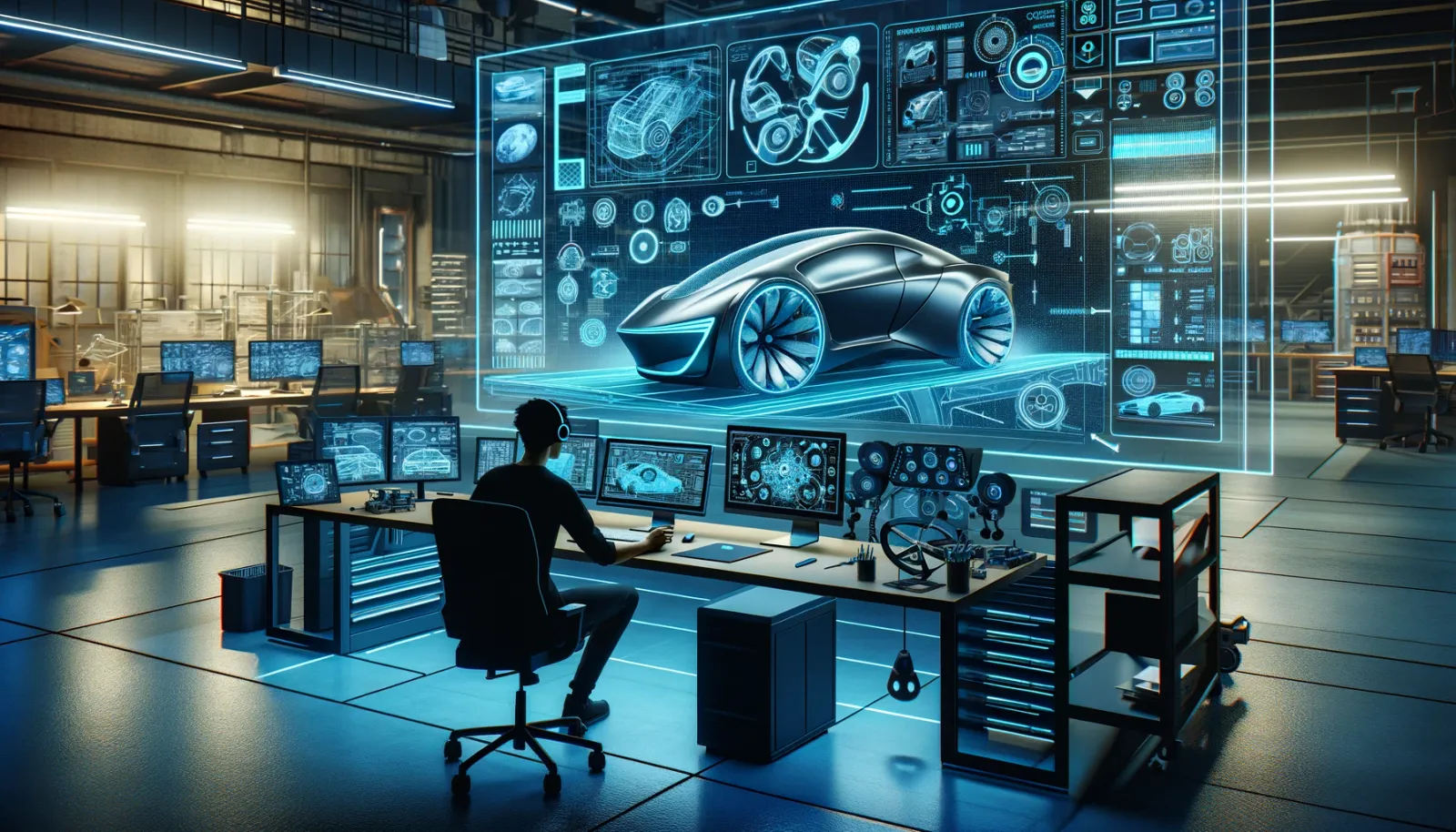
Perhaps some readers might argue that to meet the consumer demands outlined above, it is necessary to develop and manufacture SDVs. And they would be partly correct! However, only partly, as the concept of SDV implies a vehicle whose features and functions are primarily enabled through software rather than hardware. As you might have noticed, the scope of consumer demands leads a broad spectrum of changes and improvements that need to occur in the development and manufacturing of vehicles.
And this is precisely why SODA views SDV much more broadly than just changes in the internal architecture of a vehicle. Transitioning to the production of such next-generation SDVs requires changes in the following key areas of OEM operations: organizational changes and process adjustments, rethinking E/E architecture, and embracing a new software concept. Further analysis determines which of these changes in the vehicle development process contribute to meeting specific consumer requirements.
Organizational Changes and Process Adjustments
Why is there even a need to change anything in the structure of an organization like an OEM? The fact is that automotive companies have historically focused primarily on the mechanical aspects of vehicles and their advantages. In turn, the paradigm shift towards software defined functionality requires entirely different skills and expertise. Companies that already produce Software Defined Vehicles, such as Tesla and Lucid, function more like technology companies than traditional automakers.
Modern vehicle manufacturers face significant challenges in meeting these consumer expectations for swift innovation due to the constraints imposed by traditional software development models. Indeed, most use the ASPICE framework, which is based on the V-Model, in conjunction with the Waterfall approach. Such process presents a significant challenge in the realm of automotive software development due to its phase-dependent nature, rigid requirement engineering, and late testing.
Implementing agile methodologies that facilitate rapid iterations, comprehensive testing, and early and incremental release cycles allows automakers to respond more promptly to changing market demands. The study jointly conducted by SODA and VSOptima demonstrates the possibility of doubling the software development process speed by adopting the Feature-Driven Development approach and using modern tools from SODA. For more information on implementing Agile approaches in the automotive industry can be found in the next article on our blog.
Digital-first Approach in Automotive Development
Lengthy development cycles among modern automakers arise not only from following Waterfall approaches within V-Model processes but also from the manner in which the design, implementation, and validation of new vehicles or releases of embedded software with new functionalities are conducted.
Traditional vehicle development heavily relies on the creation and testing of physical prototypes, which is an expensive and time-consuming endeavor. As a result, the design and functionality of a car are traditionally tested in the late stages of the development cycle, often revealing issues that are costly and time-consuming to rectify. And even in such cases, this does not guarantee mass vehicle recalls or increased loads on service centers due to multiple malfunctions during operation, because these issues were not identified during validation on a limited number of physical prototypes or test scenarios.
If we consider the problems with testing autonomous vehicles, the situation becomes even more bleak. Autonomous vehicles need to navigate a wide range of situations and make decisions in fractions of a second, making testing in real-world conditions complex and risky. The classical approach, based on physical tests and real scenarios, cannot fully and safely test the myriad of unpredictable and potentially dangerous situations these vehicles may encounter.
Using Digital Twins from the very beginning of the vehicle development process solves all the problems outlined above! Digital Twins, being data-driven virtual models that accurately mirror physical objects, systems, or processes, enable the simulation, testing, and validation of vehicles and their components in a virtual environment well before a physical prototype is ever built. This approach significantly accelerates the development process and opens up new opportunities for enhancing vehicle safety levels. The Digital Twin allows manufacturers to explore and solve complex problems, optimize design and functionality, and conduct predictive analysis and scenario testing without the need for creating costly and labor-intensive physical prototypes.
For autonomous vehicles, Digital Twin technology is particularly beneficial as it provides a safe and effective method for simulating complex scenarios and traffic conditions that are risky to reproduce in the real world. This technology allows testing autonomous vehicles across a wide range of unpredictable and potentially dangerous situations, ensuring that these vehicles can meet the SOTIF standard.
For more information about using Digital Twins in the automotive industry, you can refer to the article - The Role of Digital Twins in Next-Generation Vehicles.
Changes in Current Vehicle Architecture
What do classical vehicle architectures currently represent, and why is there a need for change? Today, a well-equipped passenger car can contain up to a hundred ECUs, each with a specific purpose — for example, power steering, airbag activation, door locking, and so on. All of this is compounded by the presence of extensive, heavy, and expensive wire harnesses, as well as complex management of E/E component suppliers.
In general, this way of doing things works - the car is tested and certified, then it is sold over the next five years, and during these five years, the automaker will create the next car with a similar architecture. With this approach, there's only one problem - how to update such a car? In fact, it's a very challenging task - managing a hundred ECUs and ensuring zero downtime during updates. And considering that most of the functions are implemented at the hardware layer, you are left with very little functionality that can be updated remotely. It turns out that such vehicles cannot meet consumer demands, such as upgradeability, the ability to personalize the vehicle, and the constantly growing user demand for new functionality.
Software Defined Vehicle Detected
And now we've come to the moment when it's time to talk about classic SDV =) Formally speaking, an SDV is a vehicle designed using a software-centric approach that utilizes loosely coupled software components and hardware abstraction.
The term "Software Defined Vehicle" emerged quite some time ago, becoming popular in the mid-to-late 2010s to describe the evolution of cars from mechanical devices to devices primarily controlled by software. This transformation is often compared to the transformation of the smartphone (hence the phrase "smartphone on wheels"). Indeed, many years ago, phones came in a variety of shapes and sizes, with numerous functions. Now, they all are pocket rectangles, differing by the base operating system and regularly updated software. People talking about SDVs assert that a similar transformation is happening with cars, making cars "smartphones on wheels."
In other words, SDV is any vehicle whose existing functions can be upgraded over time or have entirely new ones implemented through software, instead of needing to change physical parts. This is precisely what consumers need - to have the ability to increase the functional value of the purchased car during its ownership, rather than going to buy a new one after the five-year cycle of the automaker.
Consolidation Through Zonal Architecture
We still have problems with the complexity of the E/E architecture - a large number of ECUs and connecting wiring. After all, the transition to software-based functions will only exacerbate this problem - more computing power, more sensors, and connecting wires are needed.
To address this complexity, the industry must transition to new E/E architectures for SDVs. One example of such an architecture that solves the complexity problem is zonal architecture.
Zonal architecture in the automotive industry refers to a design approach that organizes the vehicle's E/E components based on specific physical zones or areas within the vehicle. The concept of E/E zonal architecture involves the use of two new classes of devices - Central Server and Zonal Gateway. Each zone has a dedicated Zonal Gateway, which acts as a local communication hub, transmitting data through a single high-speed Ethernet channel to the backbone network. Central Servers, connected to the backbone network, acts as a hub for processing and integrating data collected from various zones. It is responsible for executing the algorithms and computations necessary for implementing complex functions.
Thus, the use of Zonal Gateways reduces the need for extensive wiring throughout the vehicle. And the use of Central Servers optimizes computational resources by consolidating physical ECUs, thereby reducing the number of hardware components and wiring, which leads to weight reduction and lower overall costs. Additionally, the scalability of functionality is enhanced by using a high-speed Ethernet communication network, which can ensure network modularity and component interchangeability.
Conclusion
According to SODA, the path to SDV is not just a technological evolution; it requires changes in development processes within OEM manufacturers and other key players in the automotive industry. The triad of changes - adopting Agile methodologies, rethinking E/E architecture, and utilizing Digital Twins in development and maintenance - forms the cornerstone of this transformation. Looking ahead, the industry's ability to implement and adapt to these changes will be crucial for meeting consumer needs for next-generation vehicles.